José Luis Moronta Chacón
Configuration & Standards Director 7 de marzo de 2022
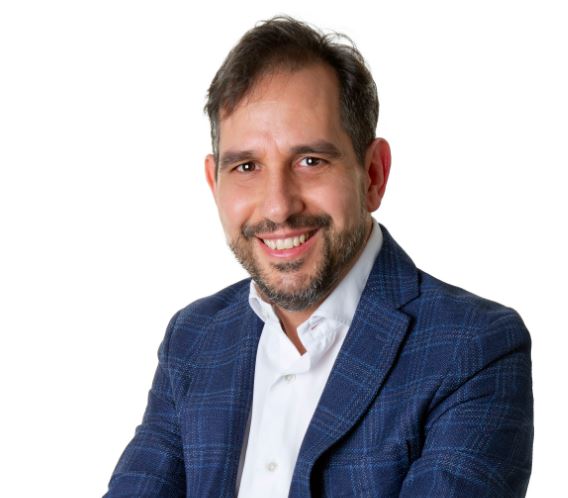
From the Technical Direction of Aernnova group, we are trying to lead a strategic view of technological development that allows us to position ourselves at the forefront of our sector. This technical view is based on the “know-how“, on how we do things in order to always try to improve them.
“To establish and maintain the consistency of the physical and functional attributes of a product throughout its life cycle”
A very important part of this leadership is a good configuration management, that great unknown that serves to establish and maintain the consistency of the physical and functional attributes of a product with its requirements, design and operational information throughout its life cycle.
If we design an item and manufacture that product for sale, we must have a plan that identifies a baseline for its development and the parts included in the design. This plan for managing changes to a product in a systematic way and for maintaining its integrity over time is called Configuration Management (CM). Configuration management establishes what design is to be used to manufacture a product, what tooling is needed, and what third-party products are needed from a specific supplier.
The configuration management process is made up of five disciplines that will establish the baseline of a product and manage any changes over time
Planning and management: Guides the design of the product, who has what responsibilities, establishes program configuration milestones and includes which tools and procedures to use.
Identification: Establishes naming standards for elements, third-party requirements, and allows establishing a product structure and a baseline of a product’s starting configuration.
Change Control: Maintains control of configurations, change requests and the execution of changes to a system and its documentation.
Status Accounting (Tracking): Involves the entire process of recording and reporting configuration item descriptions and baseline changes during the lifecycle of the item.
Verification and audits: Is capable of auditing what has been implemented and maintains control of the entire managed product.
Let’s see an example: How would a structure be affected by changes?
Any configured product structure relates the elements, parts and assemblies themselves to the elements that manage the effectiveness or applicability of the changes, i.e. the aircraft number or delivery sequential for Aernnova.
Thus, in this example containing four evolutions, the product structure in each case would be different and would apply to different effectivity ranges. Each one of the different design solutions (DS’s) carries an effectivity to all its children and in turn are related to each change that gives rise to that evolution (Change Requests – CR’s).
On the other hand, it must be taken into account that we will usually try to orient the product structures from a common technical and productive point of view. That is to say, by using concurrent engineering, the particular view of the engineering area and that of manufacturing and assembly can be agglutinated in the same structure. Maintaining this criterion when managing initial definitions and subsequent changes will always save time and effort.
As I have already pointed out, configuration management is involved in all phases of development or implementation of a change, from the offer phase in which a configuration is defined according to the contractual technical specifications, until it is manufactured and delivered. From then on, configuration management is ensured by the after-market service. In between, we must always ensure that the configuration designed (As-Designed) and planned (As-Planned) is the one we manufacture and deliver (As-Built), clearly identifying any deviations, which is the responsibility of Plant Quality or subcontracting.
Finally, I would like to emphasize what stage of development we are at and where we should be heading. Currently PLM (Product Lifecycle Management) tools such as Teamcenter are enabling us to consolidate as a CMII (Configuration Management Company) entity. Integration with a powerful ERP (Enterprise Resource Planning System) such as Infor will substantially improve the data infrastructure and access to data.
“Management tools around the cloud will allow us to move towards automation and digitalization processes that will facilitate the use of a Single Source of Data as the origin of the configuration of our products”.
The future is no longer far away. It is already here and we have a plan to consolidate our position among the best aerostructures suppliers. Welcome to the future.